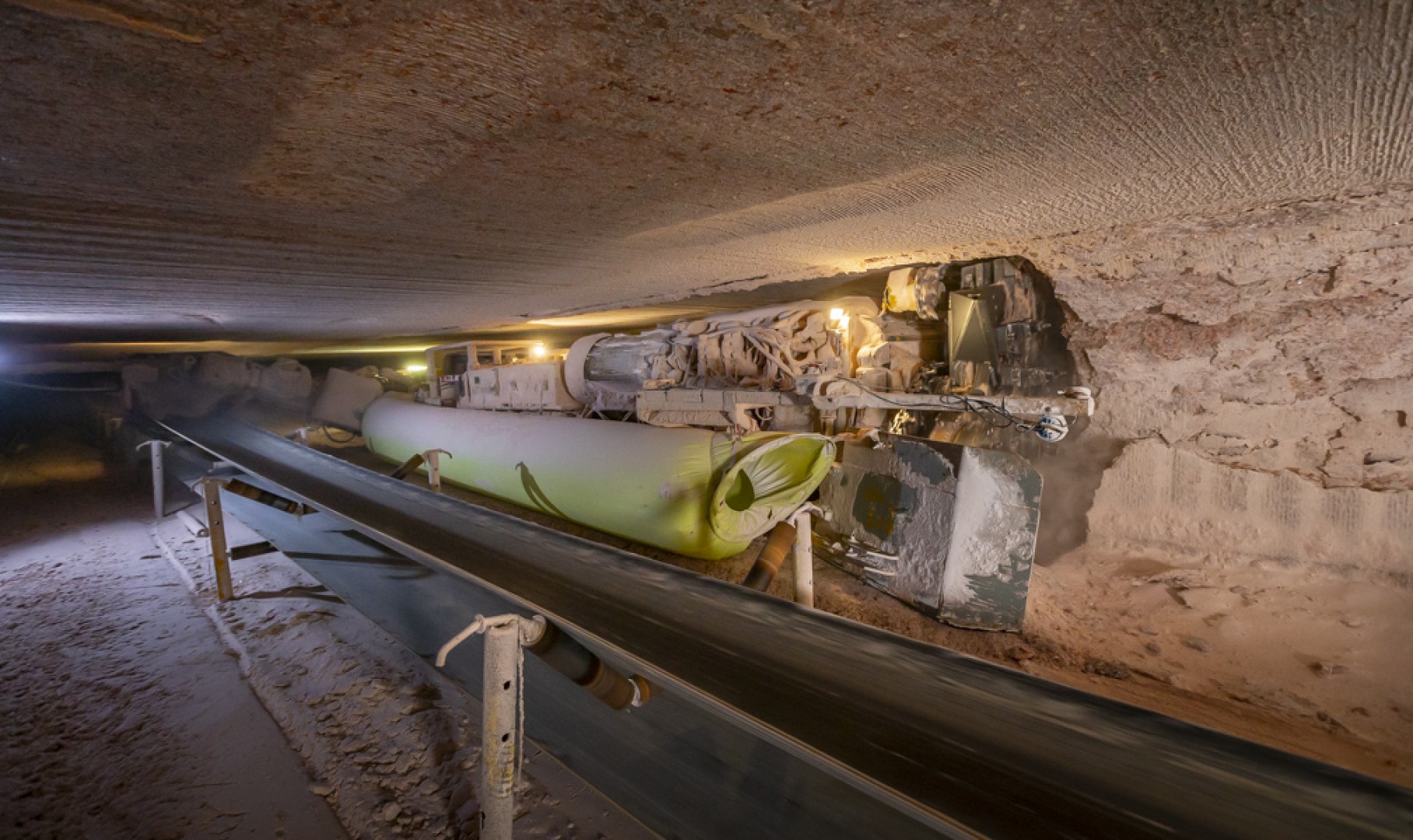
NextGEN: Remote Operations & Automation ΓÇô Bridging the Distance
Two focus areas of our NextGEN work – Integrated Operations Centers and Automation & Process Control – are coming together in new ways as we continue using technology to transform our business. Remote operation capabilities being designed into our Integrated Operations Centers and automation are enabling us to operate, monitor and manage equipment in safer, more efficient and predictable ways – sometimes from miles away or a mile above.
Remote operations and automation are crucial to the continued success of our business for many reasons, but primarily because they provide better working conditions for our employees, increase equipment runtime and improve our ability to coordinate activity across our operations.
“Being able to remotely operate equipment allows our employees to work in safer, more comfortable conditions where they have access to all the information and resources they need,” explains Chris Hagemo, Sr. Director, Digital Strategy. “Automation allows us to reduce repetitive, tedious tasks and those involving potentially hazardous work so our employees can invest their time and talent in safer and more engaging work.”
Automation plays an important role in operations at Esterhazy’s new K3 mine, allowing employees who worked in close proximity with mining machines to operate and monitor them from a safer distance or focus on other work.
The mining machines (pictured above) make three “passes” to mine an area – an initial “first pass” that sets the direction and forges a new path through rock, and two additional passes that mine ore.
The machines run autonomously for all three passes at K1 and K2 and for the second and third passes at K3. A portion of the K3 fleet will also run autonomously for the first pass by mid-year.
Mining machines are running without human intervention – with advanced instrumentation and programming we can keep the machines straight. As the mining machines advance, another automated machine installs hardware to build the conveyor belt used to transport ore from the mining areas to the surface. Running these machines without human intervention eliminates downtime, as they can safely operate 24/7.
The dispatch center on the surface being designed as our next Integrated Operations Center has communications and cameras that employees use to monitor progress of the machines so they can schedule in-person checks and start, stop or adjust them as needed to ensure safe operation and support the mine plan.