As of December 8, Esterhazy K3’s newly completed south shaft headframe is operating at full hoisting capacity. Production officially began November 8 following successful commissioning of the headframe and ore handling system in October.
“Thanks to the dedication of our team and contract partners – the south shaft headframe was safely completed approximately three months ahead of schedule,” explains Bernie Boutin, Director of Capital Projects – K3. “It was always a goal to accelerate completion of the south shaft headframe, mine ore storage bins and related conveyor systems, however the early closure of K1 and K2 made it that much more important.”ΓÇ»
Ramping Up K3’s Hoisting Capacity & Production
As planned, hoisting capacity of the south shaft headframe started at 10,000 tons per day and is increasing to 40,000 tons per day in December. Combined with the north shaft headframe, which has been in operation since 2018, this will bring K3’s hoisting capacity to more than 80,000 tons per day.
Esterhazy K3's south shaft headframe officially began production in early November. It is used solely to move potash ore to the surface. K3's north shaft headframe - which has been in operation since 2019 - is used to move potash ore to the surface and transport people and equipment.
Having the new south headframe and underground ore handling system in production removes current ore hoisting constraints and ensures capacity for additional ore supply as future mining machines are assembled and put into production.
Production at K3 is also ramping up with the addition of ore from the south shaft – reaching a new daily record of more than 43,000 tons by mid-November. Total tons will continue to increase with the recent addition of a ninth four-rotor mining machine and two more mining machines by June 2022. ΓÇ»
“With both shafts now operational, our focus remains on increasing tons to fully leverage K3’s hoisting capacity,” explains Bradley Danylko, Sr. Mine Manager. “We’ll do that by continuing to grow our fleet of mining machines and use technology to find new ways to safely, efficiently make the quality products our customers depend on.” ΓÇ»
Delivering on our Commitment to Safety
"The K3 project required in excess of 12.5 million person-hours to execute the work, and there were up to 500 persons on site per day during peak construction periods. As the K3 project commences, we're proud to report that there were ZERO reportable injuries within Capital teams over the last 12 months," said Bernie Boutin, Director of Capital Projects – K3. "Mosaic is truly grateful for all the hard work and dedication of Capital and Operations team members, Hatch and Wood PLC, and all contractor groups that helped build K3. We're proud of the future that has been built for Mosaic, for our employees and for the communities we live in."
Growing K3’s Fleet of Automated Mining Machines
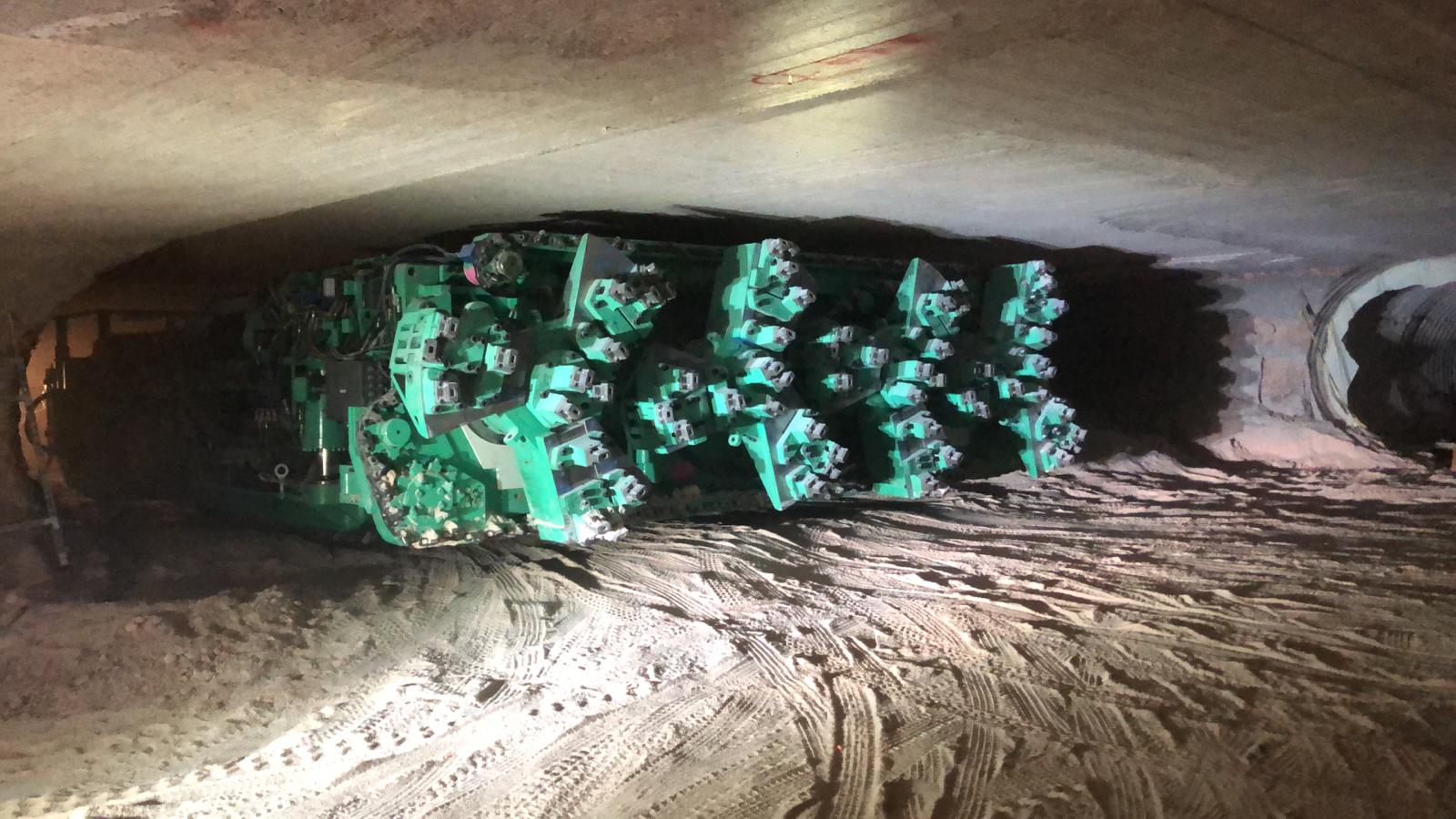
A ninth four-rotor mining machine left the shop in November and is now in production at K3.
Production at K3 is also ramping up with ore from the south shaft and the recent addition of a ninth four-rotor mining machine. Two more mining machines are expected to be in production by June 2022.
“Safely and efficiently commissioning these automated mining machines requires teamwork—especially between our assembly, maintenance, production and automation teams,” says David Steiger, Sr. Mine Manager. “Each one is assembled in the shop then trammed to mining areas to begin production.”
The machines make three passes to mine an area. On the first pass, they set the direction and forge a new path through rock while another automated machine follows behind them installing hardware to build a conveyer belt. During the second and third passes, the machines follow the path of the conveyer belt to mine ore—first on one side of the belt, then the other.
Four of the nine mining machines currently in K3’s fleet are capable of operating autonomously in all three passes, and all nine are expected to be operating autonomously for all three passes in fully developed production areas in early 2022. Running these machines with minimal human intervention reduces risk for our employees and eliminates downtime, as they can safely operate 24/7. ΓÇ»
Integrated Operations: Gaining Momentum through Collaboration
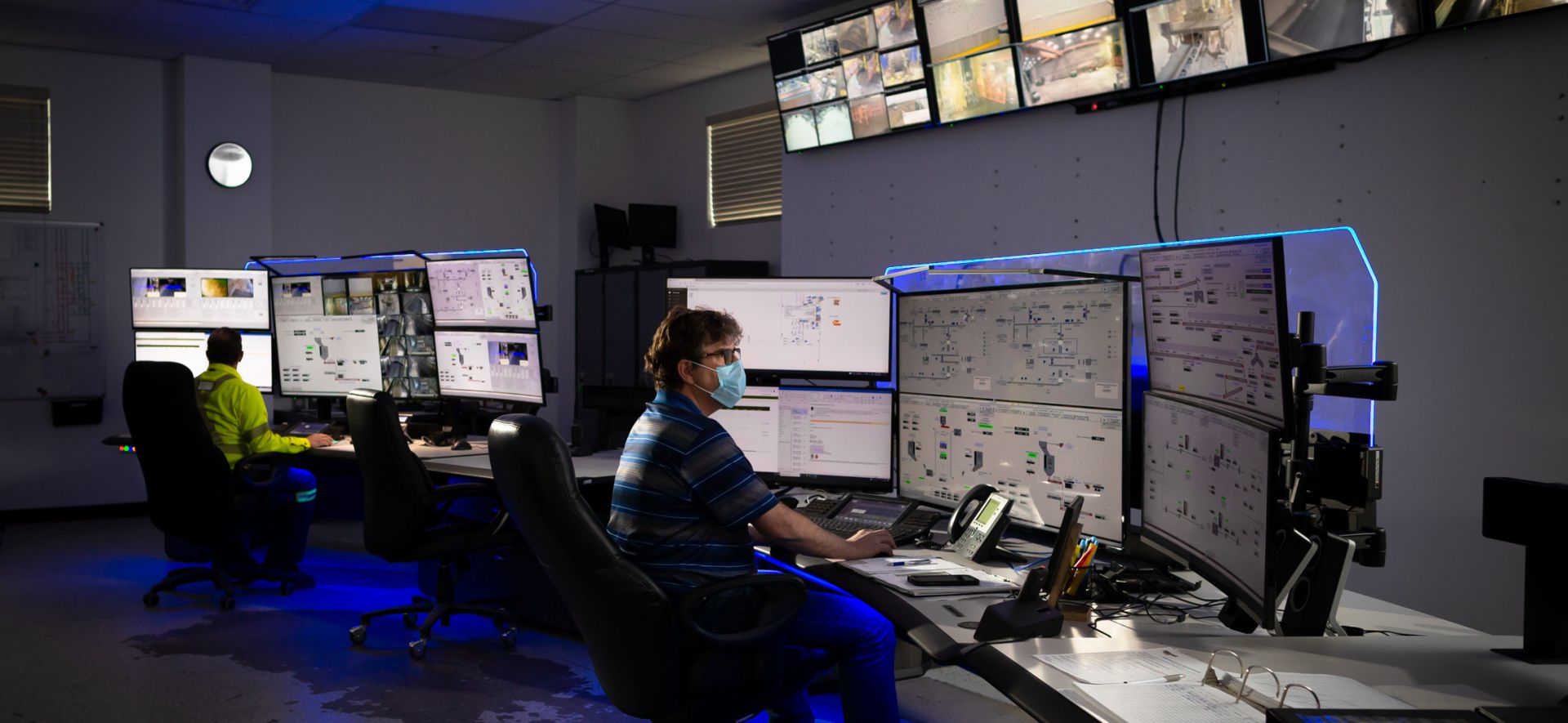
Esterhazy K3’s Integrated Operations Center (IOC) is now complete – and we’re continuing to gain momentum on integrating operations across our Esterhazy site by collaborating with the Florida mining and concentrates teams, who are also integrating operations.
“The current physical build in place is the IOC for K3—which manages the underground, hoists and ore flow to the mills,” explains Kyle Douglas, Engineer Lead. “The next step is incorporating operation of the K1 and K2 mills.”
Ultrasonic sensors are now in place for the new advanced underground conveyor control system being developed to reduce conveyor downtime and optimize miner productivity. The system coordinates the automated mining machines with the underground storage bins to maintain steady-state ore flow across the conveyor network. It allows panel miners to maximize their production rate without loading belts past their design limits. The bins that they ultimately bump into will be kept full, but without overfilling—which should lead to more continuous operation.
Another big step forward—new consoles have been installed that give us the ability to change operating screens at the touch of a single button on the smart keyboard. They provide rapid access to emergency and other priority screens, which can be integrated to allow access by the Emergency Operations Center during an emergency event.
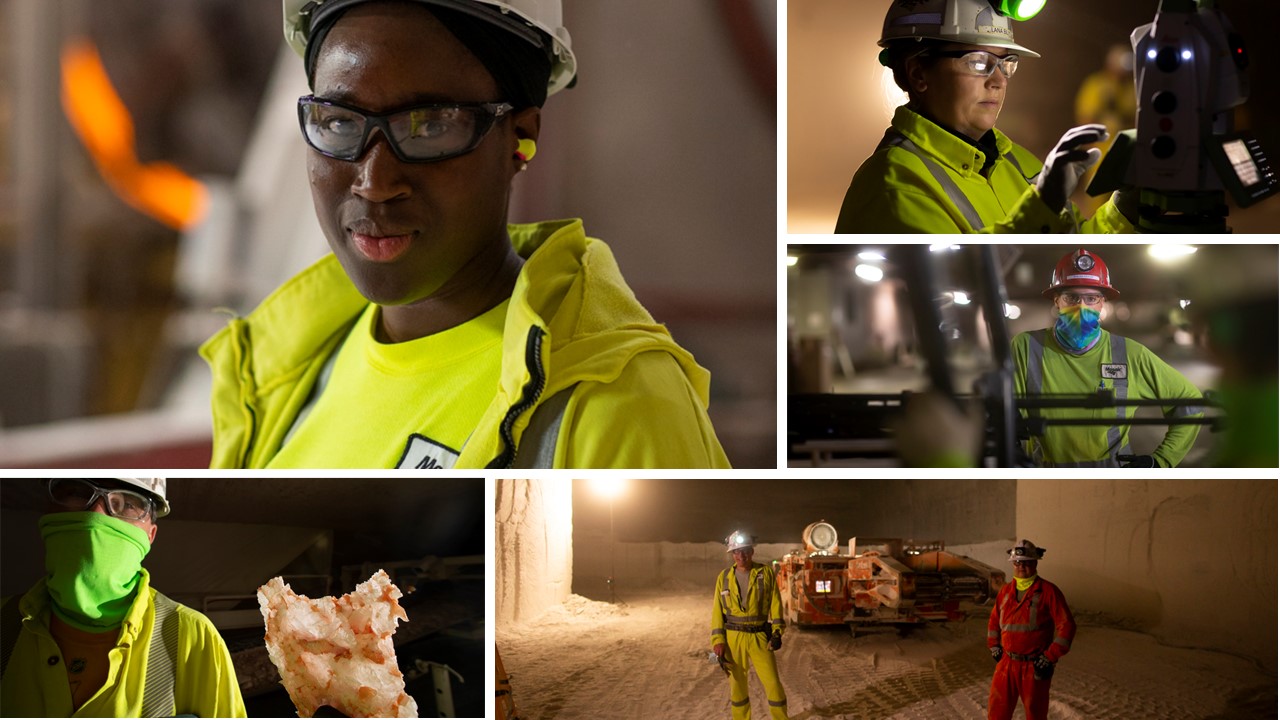
K3 Transition Workforce Plan: A Look Back
When the K3 Transition workforce plan was first developed five years ago, it predicted we could reduce our headcount by more than 200 employees if we managed our natural attrition carefully. To do this, we partnered with our local Union and developed the “K3 Transition – Hourly Workforce Plan” Letter of Understanding (LOU), which acted as our key document on how employees would move into new or changed roles as we closed our K1, K2 and Inflow operations and moved over to K3.
When K1, K2 and Inflow operations ended nine months earlier than projected, more 200 hourly employees temporarily transferred to new roles in under 10 days. A record-number of hourly roles—158 in total—were posted at one time to provide many options for employees to bid.ΓÇ»
Our workforce plan was successful because Mosaic and the Union worked continuously throughout the transition to find the best solutions and opportunities for our employees.
“Creating a workforce plan that allowed us to flex during our K3 Transition was very complex,” said Braden Domres, HR Manager - Esterhazy. “The success of this plan came from the strong partnership between our local Union Executive and our Management team and I would like to thank this group for creating a strategy that supported our employees as they shifted into new roles within our operations."